Defining “Experienced” in Flat Roofing: Experienced Flat Roof Specialists For Residential Properties
Experience in flat roofing isn’t simply a matter of years spent on the job; it’s a culmination of skills, knowledge, and exposure to a variety of challenges. A truly experienced flat roof specialist possesses a deep understanding of materials, techniques, and the intricacies of flat roof construction and maintenance, enabling them to deliver high-quality, long-lasting results.
This expertise is built over time through consistent practice, exposure to diverse projects, and a commitment to ongoing professional development. It’s not merely about the number of years worked, but the quality and complexity of the work undertaken during those years. An experienced flat roof specialist has encountered and successfully resolved a wide range of issues, from minor repairs to complex installations involving specialized materials and techniques.
Minimum Years of Experience and Project Types
Determining the minimum years of experience required to qualify as an “experienced” flat roof specialist is subjective and depends on the specific context. However, a general guideline suggests at least 5-7 years of consistent, hands-on experience in flat roof installation, repair, and maintenance. This experience should encompass a variety of projects, including both residential and potentially commercial work, depending on the specialist’s focus. The complexity of these projects should also be considered; experience with large-scale installations or challenging repairs would significantly contribute to demonstrating expertise. For example, a specialist with 7 years of experience solely installing small, single-family home roofs might not have the same level of experience as someone with 5 years working on larger, more complex multi-unit residential buildings or commercial structures. The scope and difficulty of the projects are as crucial as the years spent in the field.
Certifications and Licenses Indicating Expertise
Formal certifications and licenses serve as valuable indicators of a flat roof specialist’s expertise and commitment to professional standards. While specific requirements vary by location, several certifications and licenses can attest to a high level of proficiency. For instance, certifications from organizations like the National Roofing Contractors Association (NRCA) demonstrate a commitment to industry best practices and ongoing education. These certifications often involve rigorous testing and a proven track record of successful projects. Furthermore, some regions require contractors to obtain specific licenses to legally perform roofing work, signifying that they have met regulatory requirements and possess the necessary insurance coverage. Holding such licenses indicates compliance with local building codes and safety regulations, providing clients with an added layer of assurance. Examples of relevant licenses might include a general contractor’s license or a specialized roofing contractor’s license, depending on the legal framework of the region. These certifications and licenses act as a demonstrable validation of experience and competency.
Residential Flat Roof Materials

Choosing the right roofing material for your residential flat roof is a crucial decision impacting longevity, cost, and maintenance. Several popular options exist, each with its own set of advantages and disadvantages. Understanding these differences is key to making an informed choice that best suits your needs and budget.
Comparison of Common Residential Flat Roofing Materials
This section details the characteristics of Thermoplastic Polyolefin (TPO), Ethylene Propylene Diene Monomer (EPDM), Polyvinyl Chloride (PVC), and modified bitumen roofing membranes. We’ll examine their lifespan, cost, and maintenance requirements to aid in your selection process.
Thermoplastic Polyolefin (TPO)
TPO membranes are increasingly popular due to their durability and relatively low cost. They are composed of a blend of polypropylene and ethylene-propylene rubber, resulting in a strong, flexible, and weather-resistant material. TPO is highly resistant to UV degradation, punctures, and tears, contributing to its extended lifespan. While generally easy to install, it may require specialized equipment for larger projects. Maintenance is minimal, typically involving periodic inspections for damage and cleaning.
Ethylene Propylene Diene Monomer (EPDM)
EPDM rubber roofing has been a staple in the flat roofing industry for decades. Known for its excellent weather resistance and flexibility, EPDM is relatively easy to install and repair. It’s a cost-effective option, particularly for smaller roofs. However, EPDM can be susceptible to UV degradation over time, requiring periodic maintenance such as cleaning and potentially the application of protective coatings. Its lifespan, while generally good, is shorter than some other materials on the market.
Polyvinyl Chloride (PVC)
PVC roofing membranes are known for their exceptional durability and longevity. They offer high resistance to UV radiation, chemicals, and punctures. PVC’s strength and flexibility make it suitable for various roof designs and applications. While offering a long lifespan and low maintenance needs, the initial cost of PVC can be higher than other options. Specialized tools and expertise may be needed for installation.
Modified Bitumen
Modified bitumen roofing is a traditional, asphalt-based material often reinforced with fiberglass or polyester. It’s a relatively affordable option with a decent lifespan. Installation is typically straightforward, although it requires skilled labor to ensure proper application and prevent leaks. Regular maintenance, including inspections and repairs of any damage, is essential to maintain its watertight integrity. Its lifespan can be shorter compared to TPO or PVC, and it can become brittle over time.
Material Comparison Table
Material | Lifespan (Years) | Cost (Relative) | Maintenance Needs |
---|---|---|---|
TPO | 20-30 | Medium | Low |
EPDM | 15-25 | Low | Medium |
PVC | 25-50 | High | Low |
Modified Bitumen | 10-20 | Low | Medium-High |
Common Residential Flat Roof Issues
Residential flat roofs, while offering design advantages, are susceptible to specific problems that can lead to significant damage and costly repairs if not addressed promptly. Understanding these common issues and implementing preventative measures is crucial for maintaining a long-lasting and leak-free roof. This section will detail the most frequent problems encountered, their causes, and effective preventative strategies.
Experienced flat roof specialists for residential properties – Flat roofs, unlike sloped roofs, rely on proper drainage and watertight seals to prevent water damage. Any compromise in these critical areas can lead to a cascade of problems, ranging from minor leaks to extensive structural damage. The consequences of neglecting these issues can be severe, potentially affecting the entire building’s integrity and resulting in costly repairs or even complete roof replacement.
Leaks
Leaks are a primary concern for flat roofs. They can stem from various sources, including damaged flashing around penetrations (such as chimneys, vents, or skylights), cracks in the roofing membrane, or deteriorated sealant around seams. The consequences of unchecked leaks range from minor water stains to significant structural damage caused by water penetration into the roof deck and underlying support structures. Mold and mildew growth can also become a significant health hazard. For example, a small, unnoticed leak around a chimney flashing could eventually lead to extensive water damage in the attic, requiring costly repairs to both the roof and the interior structure.
Ponding Water
Ponding water, the accumulation of standing water on the roof surface, is another major issue. This occurs when the roof’s drainage system is inadequate or blocked by debris, causing water to pool and put excessive stress on the roofing membrane. Prolonged ponding water can lead to premature membrane failure, resulting in leaks and potential structural damage. The weight of the accumulated water can also weaken the roof structure over time. A classic example is a flat roof with a slight dip or imperfection in its design, causing water to collect in that area and eventually compromise the roof’s integrity.
Damaged Flashing
Flashing, the material used to seal around penetrations in the roof, is crucial for preventing leaks. Damaged or improperly installed flashing is a common source of leaks. Flashing can be damaged by weathering, age, or improper installation. The consequences of damaged flashing are often immediate and noticeable, leading to leaks around chimneys, skylights, or vents. For example, improperly sealed flashing around a plumbing vent can quickly lead to water damage in the surrounding areas of the roof and potentially inside the building.
Preventative Maintenance Measures
Regular preventative maintenance is vital for extending the lifespan of a residential flat roof and avoiding costly repairs.
Taking proactive steps can significantly reduce the risk of these common problems. A well-maintained roof requires less intervention and ensures a longer, more reliable service life. This ultimately translates to cost savings for homeowners.
- Regular inspections: Conduct at least two inspections annually, preferably in spring and fall, to check for signs of damage, such as cracks, blisters, or ponding water.
- Clean gutters and drains: Regularly clean gutters and downspouts to ensure proper drainage and prevent water buildup.
- Repair minor damage promptly: Address any minor damage, such as cracks or loose flashing, immediately to prevent them from escalating into larger problems.
- Professional maintenance: Schedule professional inspections and maintenance every 3-5 years to ensure the roof’s structural integrity and identify potential issues early on.
The Repair Process for Residential Flat Roofs
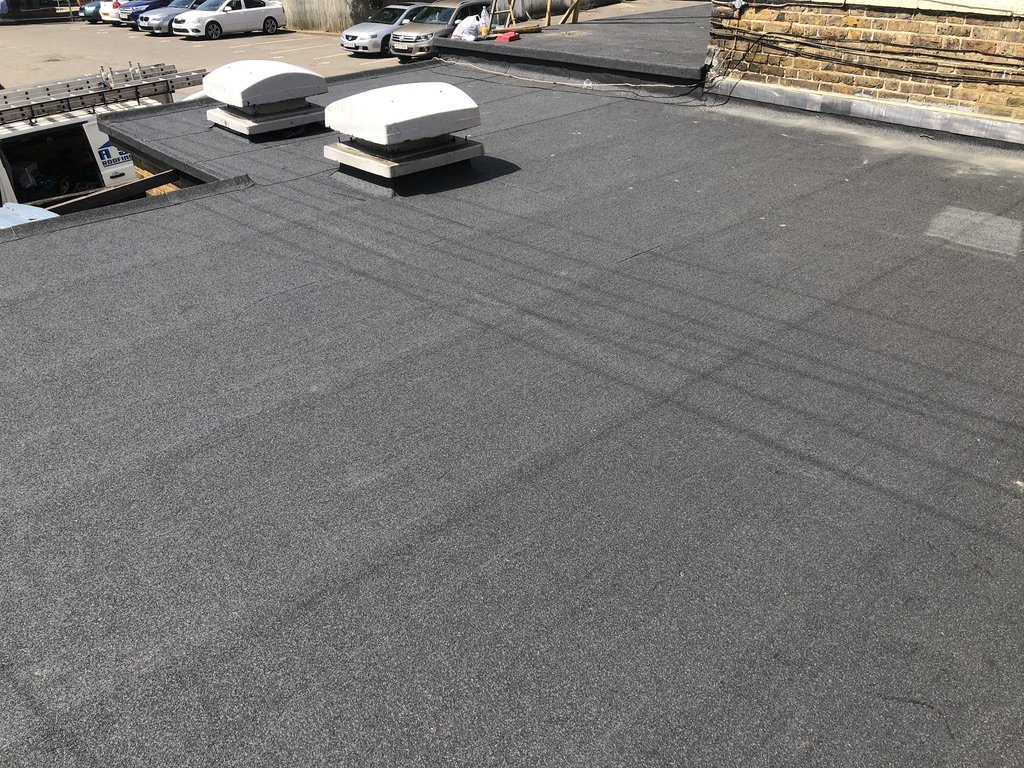
Repairing a residential flat roof requires a systematic approach to ensure longevity and prevent further damage. The process involves careful assessment, precise leak detection, and the skillful application of appropriate repair techniques. Ignoring even minor issues can lead to significant and costly problems down the line.
Leak Detection Methods
Pinpointing the source of a leak is crucial for effective repair. Several methods are employed by experienced specialists. Visual inspection often reveals obvious signs of damage, such as cracks, punctures, or blisters. However, more subtle leaks may require more advanced techniques. Moisture meters are used to detect hidden moisture within the roofing system, indicating areas of potential water ingress. Infrared thermography uses thermal imaging to identify temperature variations, which can indicate the presence of moisture and pinpoint leaks. Finally, water testing, involving controlled application of water to the roof surface, can help locate leaks not readily apparent through other methods.
Repair Techniques for Common Issues
The repair technique depends on the type and extent of the damage. For minor punctures or cracks in the roofing membrane, patching with compatible materials is often sufficient. This involves cleaning the affected area, applying a suitable adhesive, and then applying a patch that blends seamlessly with the existing membrane. For larger areas of damage or significant deterioration, a more extensive repair might be needed. This could involve removing the damaged section of the membrane and replacing it with new material, ensuring proper adhesion and sealing to prevent future leaks. Blistering, often caused by trapped moisture, requires careful removal of the blister, drying the underlying substrate, and then resealing the area. Finally, addressing damaged flashing around penetrations (chimneys, vents, etc.) is critical. This typically involves removing the old, deteriorated flashing and installing new flashing, ensuring a watertight seal around the penetration.
Tools and Equipment Used in Flat Roof Repair
Experienced flat roof specialists utilize a range of specialized tools and equipment to perform efficient and effective repairs. These include but are not limited to: safety harnesses and fall protection equipment (essential for working at heights), various types of knives and cutting tools for precise membrane cutting, specialized roofing adhesives and sealants for bonding and waterproofing, patching materials compatible with the existing roof membrane, roofing torches or heat guns for applying certain types of membrane, moisture meters to detect hidden moisture, infrared cameras for thermal imaging leak detection, various brushes and rollers for applying sealants and coatings, scaffolding or ladders for safe access to the roof surface, and finally, power tools for removing damaged sections of the roof.
Flat Roof Repair Workflow
The following flowchart illustrates the typical workflow of a flat roof repair project:
Finding and Vetting Specialists
Finding a reliable and experienced flat roof specialist requires diligent research and careful vetting. This process ensures you receive high-quality workmanship and protect your investment in your home. Taking the time to thoroughly investigate potential contractors will significantly reduce the risk of future problems and costly repairs.
Locating Experienced Specialists involves utilizing a multi-pronged approach. Combining online resources with personal recommendations provides a comprehensive search strategy.
Methods for Locating Specialists
Several avenues exist for identifying potential flat roof specialists. Online directories, such as those provided by Angie’s List or HomeAdvisor, offer a starting point, allowing you to filter results based on location, experience, and customer reviews. However, relying solely on online platforms can be limiting. Seeking referrals from trusted sources, such as friends, family, or neighbors who have recently had flat roof work done, can yield valuable insights and recommendations. Checking with local building supply stores or contacting your homeowner’s association can also uncover reputable contractors in your area. Finally, reviewing online business listings and checking for certifications and licenses can offer an initial assessment of the company’s credentials.
Crucial Questions for Initial Consultations
The initial consultation serves as a crucial opportunity to assess the specialist’s expertise and suitability for your project. Asking specific questions demonstrates your proactive approach and helps determine if their skills and experience align with your needs. For instance, inquiring about their experience with specific flat roof materials relevant to your property is essential. Understanding their approach to problem diagnosis and repair, as well as their warranty policies and insurance coverage, provides valuable information. Discussions regarding project timelines, cost estimates, and payment schedules should also be thoroughly explored. Finally, requesting references from previous clients allows for independent verification of their work quality and professionalism.
Checklist for Verifying Qualifications and Credentials
Before committing to a specialist, a thorough review of their qualifications and credentials is paramount. This includes verifying their licensing and insurance, confirming their years of experience specifically with residential flat roofs, and examining customer reviews and testimonials. A reputable contractor will readily provide proof of their licensing and insurance coverage, which should be current and valid. Their experience should extend beyond general roofing; it’s crucial to verify their expertise with flat roofs. Finally, independent verification of their work through online reviews or direct contact with previous clients adds an additional layer of assurance. A comprehensive checklist should include confirmation of their business license, proof of liability and workers’ compensation insurance, and a portfolio showcasing past projects similar in scope and material to your own.
Cost Estimation and Budgeting
Accurately estimating the cost of flat roof repair or replacement is crucial for effective budgeting and avoiding unexpected expenses. Several factors significantly influence the final price, making a thorough assessment essential before commencing any work. Understanding these variables allows homeowners to make informed decisions and find the best value for their investment.
Several key factors contribute to the overall cost of flat roof repair or replacement. These factors interact to create a unique cost for each project, and it’s important to understand how each impacts the final price. Ignoring these factors can lead to significant budget overruns.
Factors Influencing Flat Roof Repair/Replacement Costs
The cost of flat roof repair or replacement varies considerably depending on several key factors. These factors can significantly impact the overall project budget, making it essential to consider them carefully during the planning phase.
- Roof Size and Complexity: Larger roofs naturally require more materials and labor, increasing the overall cost. Complex roof designs with multiple levels or unusual features also add to the expense.
- Type of Repair or Replacement: Simple repairs, such as patching minor leaks, are significantly cheaper than a complete roof replacement. The extent of damage and the necessary work directly influence the cost.
- Materials Used: Different roofing materials vary greatly in price. EPDM rubber, TPO, and PVC membranes, for example, have different price points, affecting the overall project cost. Higher-quality, longer-lasting materials generally command a higher price but can offer better long-term value.
- Labor Costs: Labor costs vary depending on location, the contractor’s experience, and the complexity of the job. Specialized skills or the need for extra personnel can increase labor costs.
- Accessibility and Location: Difficult-to-access roofs, such as those on multi-story buildings or those requiring specialized equipment, will incur additional costs. Remote locations may also impact the overall price due to travel time and expenses.
- Permits and Inspections: Necessary permits and inspections add to the overall cost. These fees vary by location and the scope of the project.
- Existing Roof Condition: The condition of the existing roof significantly impacts the cost. A roof requiring extensive preparation or removal before installation will be more expensive than one in relatively good condition.
Cost Ranges for Different Repairs and Materials
Providing exact cost ranges is difficult without specific project details, but general estimates can offer a helpful benchmark. These estimates should be considered as broad guidelines and are subject to significant variation based on the factors listed above.
- Minor Repairs (Patching Leaks): $300 – $1500
- Moderate Repairs (Replacing Sections): $1500 – $5000
- Complete Roof Replacement (EPDM): $5000 – $15000 (for a typical residential roof)
- Complete Roof Replacement (TPO or PVC): $7000 – $20000 (for a typical residential roof)
These figures are based on average costs and may vary significantly depending on the factors previously discussed. Always obtain multiple quotes to compare prices and services.
Sample Budget Breakdown for a Hypothetical Flat Roof Repair
Let’s consider a hypothetical scenario: a 1000 square foot residential flat roof needing repair due to several small leaks and some minor damage to the existing EPDM membrane.
Item | Cost |
---|---|
Material Costs (EPDM membrane, adhesive, flashing, etc.) | $2000 |
Labor Costs (removal of damaged sections, preparation, installation) | $3000 |
Permitting and Inspections | $500 |
Contingency (10% for unforeseen expenses) | $500 |
Total Estimated Cost | $6000 |
This is a simplified example. A more comprehensive budget might include additional items like debris removal, disposal fees, and potential repairs to underlying structures. Always discuss a detailed breakdown with your chosen contractor.
Warranties and Guarantees
Choosing a flat roof specialist involves significant investment, both financially and in terms of protecting your home. Therefore, understanding the warranties and guarantees offered is crucial for ensuring long-term peace of mind and protecting your investment. A comprehensive warranty acts as a safeguard against potential defects in materials or workmanship, offering recourse should problems arise.
Warranties provide legal protection for consumers and help establish the credibility and confidence of the contractor. They define the responsibilities of both the contractor and the homeowner, outlining the terms and conditions under which repairs or replacements will be provided. The absence of a robust warranty should raise concerns about the specialist’s commitment to quality and their long-term accountability.
Types of Warranties
Different warranties cover different aspects of the roofing project. Understanding these distinctions is key to comparing offers from various specialists.
- Material Warranties: These warranties cover defects in the materials themselves, such as the roofing membrane, insulation, or flashing. Manufacturers typically provide these warranties, and their length can vary significantly, ranging from 10 to 20 years or even longer, depending on the material’s quality and the manufacturer’s confidence in its durability. For example, a high-quality TPO membrane might come with a 20-year warranty, while a less expensive alternative might only offer a 10-year warranty.
- Labor Warranties: These warranties cover the workmanship of the roofing specialist. They guarantee that the installation was performed correctly and to the required standards. Labor warranties are typically provided by the contractor and their duration often matches or slightly exceeds the material warranty. A common labor warranty might be for 5 years, guaranteeing that the installation will be free from defects in workmanship for that period.
- Combined Warranties: Some specialists offer combined warranties that cover both materials and labor. This simplifies the process in case of issues, as you only need to deal with one party for repairs or replacements under the warranty terms. A combined warranty might cover both materials and labor for 10 years, providing comprehensive protection for a significant portion of the roof’s lifespan.
Key Aspects to Consider When Reviewing a Warranty
Before signing a contract, carefully examine the warranty’s fine print. Several key elements should be thoroughly reviewed to avoid potential misunderstandings or limitations later.
- Warranty Duration: The length of the warranty is a crucial factor. Longer warranties generally indicate greater confidence in the materials and workmanship.
- Coverage Details: Precisely understand what the warranty covers and what it excludes. Some warranties may exclude damage caused by specific events (e.g., extreme weather, neglect). Others may have limitations on the extent of coverage, such as a prorated coverage after a certain number of years.
- Transferability: Check if the warranty is transferable to a future homeowner if you plan to sell your property. This adds significant value to your home and protects the investment for subsequent owners.
- Claim Process: Understand the procedure for filing a warranty claim, including required documentation and the timeframe for resolution. A clear and straightforward claim process is essential for a smooth experience if problems arise.
- Contact Information: Ensure the warranty clearly states the contact information of the party responsible for handling warranty claims. This could be the manufacturer, the contractor, or a third-party administrator.
Safety Precautions During Flat Roof Work
Working on a flat roof presents unique safety challenges due to the height, potential for falls, and exposure to the elements. Proper safety procedures are crucial for both the roofing professionals and homeowners to prevent accidents and injuries. This section details the necessary precautions and equipment to ensure a safe working environment.
Flat roof work involves significant risks, primarily falls from height. Other hazards include exposure to extreme weather conditions (heat, cold, rain, wind), contact with sharp materials (metal flashing, broken tiles), and potential electrical hazards if working near power lines. Furthermore, the roof surface itself can be slippery when wet or covered with debris, increasing the risk of slips and falls. Proper planning and the use of appropriate safety equipment are essential to mitigate these risks.
Potential Safety Hazards on Flat Roofs
Several factors contribute to the inherent dangers associated with flat roof work. These hazards need to be carefully assessed and addressed before any work commences. Understanding these risks is the first step towards ensuring a safe working environment.
- Falls from height: This is the most significant risk, accounting for a large percentage of roofing accidents. The lack of a steep incline makes it easy to lose balance and fall.
- Slippery surfaces: Wet or icy conditions can render a flat roof extremely treacherous. Even seemingly dry surfaces can become slippery due to accumulated dust or debris.
- Exposure to the elements: Extreme heat, cold, rain, and strong winds can create dangerous and uncomfortable working conditions, potentially leading to fatigue and accidents.
- Sharp materials and tools: Working with sharp materials like metal flashing, broken tiles, and cutting tools requires caution to avoid cuts and injuries.
- Electrical hazards: Proximity to power lines and electrical equipment poses a significant risk of electrocution.
- Working at heights: The physical exertion and strain of working at height can increase the risk of accidents.
Safety Procedures and Equipment
Implementing appropriate safety procedures and using the correct equipment are vital for mitigating the risks associated with flat roof work. A comprehensive safety plan should be in place before any work begins.
- Fall protection systems: Harness systems, safety nets, and guardrails are essential to prevent falls from height. These systems should be properly installed and regularly inspected.
- Proper footwear: Workers should wear non-slip, steel-toed boots to provide protection and enhance stability on the roof surface.
- Personal Protective Equipment (PPE): This includes hard hats, safety glasses, gloves, and high-visibility clothing to protect against various hazards.
- Weather monitoring: Work should be suspended during severe weather conditions such as thunderstorms, high winds, or icy surfaces.
- Proper training and supervision: All workers should receive adequate training in safe working practices and the use of safety equipment. Experienced supervision is essential.
- Emergency procedures: A clear emergency plan should be in place, including communication procedures and access for emergency services.
Safety Guidelines for Homeowners
Homeowners should also take precautions during flat roof repairs or replacements. Their safety is equally important throughout the process.
- Clear the work area: Remove any obstructions from the roof area to prevent tripping hazards.
- Keep children and pets away: Restrict access to the roof during the repair or replacement process.
- Communicate with the contractors: Discuss safety procedures and ensure they are being followed.
- Inspect the work area after completion: Check for any remaining hazards once the work is finished.
- Report any concerns: Immediately report any safety concerns to the contractors.
Understanding Contracts and Agreements
A well-defined contract is crucial for a successful flat roof repair or replacement project. It safeguards both the homeowner and the roofing specialist, outlining the scope of work, payment terms, and responsibilities. A clear contract minimizes misunderstandings and potential disputes, ensuring a smooth and satisfactory experience for all parties involved.
A comprehensive contract should include several key clauses to protect both parties’ interests. Failing to have a detailed and legally sound contract can lead to significant financial and legal complications for both the homeowner and the contractor.
Sample Flat Roof Repair/Replacement Contract
This sample contract is for illustrative purposes only and should not be used as a legal document without review by legal counsel. Always consult with an attorney to ensure the contract adequately addresses your specific circumstances and complies with local laws.
CONTRACT FOR FLAT ROOF REPAIR/REPLACEMENT SERVICES
This Agreement is made this [Date] between [Homeowner Name], residing at [Homeowner Address] (“Homeowner”), and [Contractor Name], residing at [Contractor Address] (“Contractor”).
1. Scope of Work: The Contractor agrees to [Clearly describe the work to be done, including specific materials, dimensions, and any other relevant details. For example: “repair the existing flat roof using a modified bitumen system, covering an area of 500 square feet, including the removal and disposal of existing roofing materials, and the installation of new underlayment, flashing, and roofing membrane.”].
2. Payment Terms: The Homeowner agrees to pay the Contractor a total sum of [Total Price] for the completed work. Payment will be made as follows: [Specify payment schedule, e.g., 25% upon signing, 50% upon completion of the underlayment, and 25% upon final inspection and completion].
3. Timeline: The Contractor agrees to commence work on [Start Date] and complete the work within [Number] days, weather permitting. Any delays caused by unforeseen circumstances will be communicated to the Homeowner in writing.
4. Materials: The Contractor will use [Specify materials and brands, including manufacturer’s warranties].
5. Warranties: The Contractor warrants that all work will be performed in a workmanlike manner and free from defects in materials and workmanship for a period of [Number] years. This warranty excludes damage caused by [Specify exclusions, e.g., acts of God, negligence by the homeowner].
6. Permits and Inspections: The Contractor is responsible for obtaining all necessary permits and ensuring that the work passes all required inspections.
7. Dispute Resolution: Any disputes arising from this agreement will be resolved through [Specify method of dispute resolution, e.g., mediation, arbitration].
8. Termination: Either party may terminate this agreement with [Number] days written notice.
IN WITNESS WHEREOF, the parties have executed this agreement as of the date first written above.
_________________________ _________________________
Homeowner Signature Contractor Signature
Key Contract Clauses
Several crucial clauses should be included in any flat roof contract to ensure clarity and protect both parties. These include a detailed description of the work, precise payment terms, a clear timeline for completion, specifications for materials used, warranty information, provisions for permits and inspections, and a method for resolving disputes. The inclusion of a force majeure clause addressing unforeseen circumstances beyond either party’s control is also advisable. Furthermore, a clause outlining the process for handling change orders (any alterations to the original scope of work) is essential to avoid future conflicts.
Importance of Understanding Contract Terms
Before signing any contract, it is paramount that both the homeowner and the contractor thoroughly understand all terms and conditions. This includes reviewing all clauses carefully, asking clarifying questions if needed, and seeking independent legal advice if necessary. Signing a contract without full comprehension can lead to significant problems down the line, potentially resulting in costly disputes and legal battles. A clear understanding of the contract protects both parties’ rights and responsibilities, ensuring a smooth and satisfactory project outcome.
Post-Repair Maintenance and Inspection
Investing in a professional flat roof repair is a significant step towards protecting your home. However, the longevity and performance of your repaired roof depend significantly on proper post-repair maintenance and regular inspections. This section Artikels crucial steps homeowners can take to maximize the lifespan of their flat roof investment.
Regular maintenance and professional inspections are essential for ensuring the long-term health and performance of your flat roof. Neglecting these can lead to costly repairs or even complete roof replacement down the line. Proactive care significantly reduces the likelihood of unforeseen problems and extends the life of your roof investment.
Routine Maintenance Tasks
Homeowners can contribute significantly to the longevity of their flat roof through simple, regular maintenance. These tasks help identify minor issues before they escalate into major problems, saving both time and money.
- Regular Cleaning: Remove debris such as leaves, branches, and dirt from the roof surface at least twice a year, preferably in spring and autumn. This prevents clogging of drainage systems and reduces the risk of water damage.
- Gutter and Downspout Inspection: Clean gutters and downspouts regularly to ensure free-flowing water. Clogged gutters can lead to water pooling on the roof, causing damage to the membrane and underlying structure.
- Visual Inspection: Conduct a monthly visual inspection of the roof surface, checking for any signs of damage, such as cracks, blisters, punctures, or loose seams. Early detection is key to preventing costly repairs.
- Moisture Monitoring: In areas prone to high humidity, consider using a moisture meter to check for any signs of water penetration. Early detection of moisture can prevent mold growth and structural damage.
Importance of Regular Specialist Inspections
While routine homeowner maintenance is crucial, regular inspections by experienced flat roof specialists are equally important. These professionals possess the expertise to identify subtle signs of deterioration that may be missed during a casual visual inspection.
Regular inspections, ideally annually, allow specialists to detect and address minor problems before they become major, costly repairs. This proactive approach saves homeowners significant expenses in the long run and ensures the roof remains in optimal condition. A typical inspection will involve a thorough visual examination of the entire roof surface, checking for signs of wear, tear, and potential leaks. They may also use specialized equipment to assess the integrity of the roofing membrane.
Signs Requiring Professional Attention, Experienced flat roof specialists for residential properties
Several indicators suggest the need for professional attention after a flat roof repair, even if the initial repair appears successful. Prompt action on these signs prevents small issues from escalating into large, expensive problems.
- Persistent Leaks: If leaks persist despite a previous repair, it’s crucial to contact a specialist immediately to determine the underlying cause and implement a proper solution.
- Sagging or Bubbling: Noticeable sagging or bubbling in the roofing membrane indicates potential damage or moisture accumulation beneath the surface. This requires prompt professional attention to prevent further deterioration.
- Visible Cracks or Tears: New cracks or tears appearing after a repair indicate potential issues with the repair itself or underlying structural problems. A specialist can assess the extent of the damage and recommend appropriate repairs.
- Unusual Staining: The appearance of unusual staining on the ceiling or walls below the flat roof is a clear sign of a leak or water penetration that requires immediate professional attention.
FAQ Compilation
What is the average lifespan of a flat roof?
The lifespan of a flat roof varies greatly depending on the materials used, climate, and maintenance. However, you can generally expect a lifespan ranging from 15 to 30 years.
How can I tell if my flat roof needs repair?
Signs of needing repair include leaks, ponding water, visible cracks or damage, sagging areas, and missing or damaged flashing.
What are the common causes of flat roof leaks?
Common causes include damaged flashing, punctures, poor installation, ponding water, and deterioration of roofing materials due to age or weather exposure.
Are there any DIY repairs I can safely attempt?
Minor repairs like patching small cracks might be attempted by a skilled DIYer, but major repairs or replacements should always be left to experienced professionals for safety and warranty reasons.