Finding Local Contractors
Locating reliable asphalt shingle roofing contractors in your area is crucial for a successful and long-lasting roof installation or repair. This process involves utilizing various resources, verifying credentials, and comparing qualifications to ensure you choose the best contractor for your needs. This section will guide you through these essential steps.
Locating Asphalt Shingle Roofing Contractors
Several online and offline resources can help you find local asphalt shingle roofing contractors. Starting your search online offers a broad reach and allows for easy comparison.
Finding the best asphalt shingle roofing contractors nearby – Websites and resources for finding local contractors include:
- Online Directories: Yelp, Angie’s List, HomeAdvisor, and Nextdoor often feature local contractor reviews and ratings.
- Search Engines: Using search terms like “asphalt shingle roofing contractors [your city/zip code]” in Google, Bing, or other search engines will yield numerous results.
- Manufacturer Websites: Some asphalt shingle manufacturers have contractor locator tools on their websites, connecting you with installers who work with their products.
- Local Building Supply Stores: These stores often have relationships with local contractors and can provide referrals.
Verifying Contractor Licensing and Insurance
It is imperative to verify that potential contractors hold the necessary licenses and insurance before engaging their services. This protects you from potential legal and financial liabilities.
Methods for verifying licensing and insurance include:
- Check State Licensing Boards: Most states have a licensing board for contractors. You can typically search their online database using the contractor’s name or license number to confirm their license status and validity.
- Request Proof of Insurance: Ask potential contractors for proof of general liability and workers’ compensation insurance. This documentation should show current coverage and details of the insurance provider.
- Contact the Insurance Provider Directly: You can verify the validity of the insurance certificate by contacting the insurance company listed on the provided documentation.
Comparing Contractor Qualifications
Once you have a shortlist of potential contractors, it’s essential to compare their qualifications to make an informed decision. This involves reviewing their experience, certifications, and customer feedback.
The following table compares key contractor qualifications:
Contractor Name | Years of Experience | Certifications (e.g., GAF Master Elite, CertainTeed SELECT ShingleMaster) | Customer Reviews (Average Rating) |
---|---|---|---|
Contractor A | 15 | GAF Master Elite, CertainTeed SELECT ShingleMaster | 4.8 stars |
Contractor B | 8 | None | 4.2 stars |
Contractor C | 20 | GAF Master Elite | 4.5 stars |
Contractor D | 5 | None | 3.9 stars |
Evaluating Contractor Credentials
Choosing the right asphalt shingle roofing contractor is a significant investment, impacting both your home’s value and your peace of mind. Thoroughly evaluating a contractor’s credentials is crucial to ensuring a successful project and avoiding potential problems down the line. This involves more than just comparing prices; it requires a diligent examination of their experience, licensing, insurance, and reputation.
Checking references and reviewing online feedback provides invaluable insights into a contractor’s past performance and reliability. These sources offer firsthand accounts of their work quality, professionalism, and adherence to timelines. A pattern of positive feedback suggests a higher likelihood of a positive experience, while negative reviews should be carefully considered and investigated further. The absence of online reviews, however, may also be a red flag, suggesting a lack of transparency or limited experience.
Contractor Licensing and Insurance Verification
Verifying a contractor’s license and insurance is a non-negotiable step in the selection process. Contact your state’s licensing board or contractor’s state registration board to confirm that their license is valid, current, and in good standing. This verification ensures the contractor meets the minimum requirements for competency and legal operation within your jurisdiction. Similarly, request proof of liability insurance and workers’ compensation insurance. Liability insurance protects you from financial responsibility in case of accidents or damages during the project, while workers’ compensation insurance safeguards the contractor’s employees in the event of on-site injuries. Failure to verify these documents could leave you financially vulnerable. For example, if a contractor lacks liability insurance and damages your property, you would be responsible for the repair costs.
Contractor Certifications
Several certifications can indicate a contractor’s expertise in asphalt shingle roofing. While not all certifications are created equal, they can signal a commitment to professional development and adherence to industry best practices. For example, certifications from organizations like the National Roofing Contractors Association (NRCA) or specific manufacturer certifications demonstrate a contractor’s understanding of roofing techniques and materials. These certifications often involve rigorous training and testing, ensuring a higher standard of workmanship. A contractor with multiple relevant certifications often signifies a higher level of expertise and commitment to quality than one without any. Comparing certifications across different contractors allows for a more informed decision, enabling you to choose a contractor with demonstrable skills and knowledge relevant to your specific roofing needs. It’s important to understand that while certifications are a positive indicator, they are not a guarantee of perfect workmanship. Thorough vetting remains crucial.
Understanding Cost Estimates
Obtaining accurate cost estimates is crucial for budgeting your asphalt shingle roofing project. A transparent and detailed estimate allows you to compare bids effectively and avoid unexpected expenses during the installation process. Understanding the components of a cost estimate will empower you to make informed decisions.
Asphalt shingle roofing costs are influenced by a variety of factors, making direct comparisons between contractors challenging but necessary. A thorough understanding of these factors will enable you to evaluate the reasonableness of each estimate you receive.
Sample Cost Breakdown for Asphalt Shingle Roofing
The following is a sample cost breakdown for a hypothetical 2,000 square foot asphalt shingle roofing project. Remember that actual costs will vary significantly based on location, materials chosen, and the complexity of the job.
Item | Cost |
---|---|
Materials (Asphalt shingles, underlayment, flashing, nails, etc.) | $6,000 |
Labor (Tear-off, installation, cleanup) | $8,000 |
Permits and Inspections | $500 |
Waste Removal | $200 |
Subtotal | $14,700 |
Contingency (10% for unforeseen issues) | $1,470 |
Total Estimated Cost | $16,170 |
Factors Influencing Asphalt Shingle Roofing Costs
Several key factors significantly impact the overall cost of an asphalt shingle roofing project. These factors should be carefully considered when comparing estimates from different contractors.
These factors include, but are not limited to, the size of the roof, the complexity of the roof (e.g., multiple levels, dormers, valleys), the type and quality of asphalt shingles selected (architectural shingles are generally more expensive than 3-tab shingles), the need for roof repairs or replacement of underlying structures, the cost of labor in your region, and the disposal costs for the old roofing materials.
Comparison of Pricing Structures from Different Contractors
Contractors may structure their pricing differently. Some may provide a single lump-sum price, while others might itemize materials and labor separately. Discrepancies in pricing can arise from differences in the scope of work, the quality of materials used, the level of experience and expertise of the crew, and the inclusion of contingency costs. For example, one contractor might include a 10% contingency, while another might not, leading to a significant difference in the final price. Always carefully review the detailed breakdown provided by each contractor to understand what is included and excluded in their price. Direct comparison of the cost of materials and labor can reveal significant differences in value. Consider requesting a detailed breakdown of the materials specified and their unit costs. Transparency in pricing is a crucial indicator of a reliable contractor.
Contractual Agreements: Finding The Best Asphalt Shingle Roofing Contractors Nearby
A well-defined contract is crucial for a successful roofing project. It protects both the homeowner and the contractor, ensuring clarity on expectations, responsibilities, and payment terms. A comprehensive contract minimizes misunderstandings and potential disputes, leading to a smoother and more satisfactory experience for all parties involved.
A detailed and well-written contract serves as a legally binding agreement outlining the scope of work, payment terms, and dispute resolution mechanisms. This ensures that both parties understand their obligations and rights, fostering trust and transparency throughout the project. Ignoring this critical step can lead to significant complications and financial losses later.
Essential Contract Clauses
Including specific clauses in the roofing contract safeguards both the homeowner and the contractor. These clauses provide a clear framework for the project, addressing potential issues before they arise. Omitting crucial details can leave room for misinterpretations and disputes.
- Project Scope: A detailed description of all work to be performed, including materials, specifications, and any exclusions. This should be specific enough to avoid ambiguity. For example, instead of “roof repair,” the contract should specify the number of squares to be replaced, the type of shingles, and the extent of any underlayment work.
- Payment Schedule: A clear Artikel of payment milestones tied to specific stages of completion. This prevents disputes over payment and ensures the contractor receives timely compensation for their work. A typical schedule might include a down payment, progress payments at key stages (e.g., after tear-off, during installation, upon completion), and a final payment upon project completion and inspection.
- Project Timeline: Realistic start and completion dates, including allowances for potential weather delays. The contract should clearly state what constitutes a delay and how it will be handled. For instance, the contract could stipulate that the contractor must notify the homeowner of any anticipated delays within a certain timeframe and provide a revised timeline.
- Warranty Information: Details on the warranty provided for materials and workmanship, including the duration and coverage. This ensures that the homeowner is protected against defects in materials or workmanship for a specified period.
- Dispute Resolution: A clear process for resolving disputes, such as mediation or arbitration, to avoid costly and time-consuming litigation. This might involve agreeing to use a mutually acceptable mediator or arbitration service.
- Permitting and Inspections: Clarification of who is responsible for obtaining necessary permits and scheduling inspections. This should specify the contractor’s responsibility for ensuring compliance with all building codes and regulations.
- Insurance and Liability: Confirmation that the contractor carries appropriate liability and workers’ compensation insurance. This protects the homeowner from potential liability in case of accidents or injuries on their property.
Clearly Defined Payment Schedules and Project Timelines
Clear payment schedules and project timelines are fundamental to a successful roofing project. They ensure timely payments to the contractor and a predictable completion date for the homeowner. Ambiguity in these areas can lead to disputes and delays.
A well-structured payment schedule should be directly tied to specific, measurable milestones in the project. For example, a portion of the payment might be released upon completion of the tear-off, another after the underlayment is installed, and the final payment upon project completion and satisfactory inspection. Similarly, the project timeline should be realistic, considering potential weather delays or material availability issues. Including specific dates or ranges for each phase of the project ensures both parties are on the same page.
Dispute Resolution Process
A clearly defined dispute resolution process is crucial for managing disagreements that may arise during a roofing project. It provides a structured approach to resolving conflicts, preventing escalation and potential legal battles.
The contract should Artikel a specific process for handling disputes, such as mediation or arbitration. Mediation involves a neutral third party facilitating communication and helping the parties reach a mutually agreeable solution. Arbitration involves a neutral third party hearing evidence and making a binding decision. Both options are generally less expensive and time-consuming than litigation. The contract should specify which method will be used, the selection process for the mediator or arbitrator, and the rules governing the process. For example, the contract could specify that any disputes will be resolved through binding arbitration using the rules of the American Arbitration Association.
Project Timeline and Management
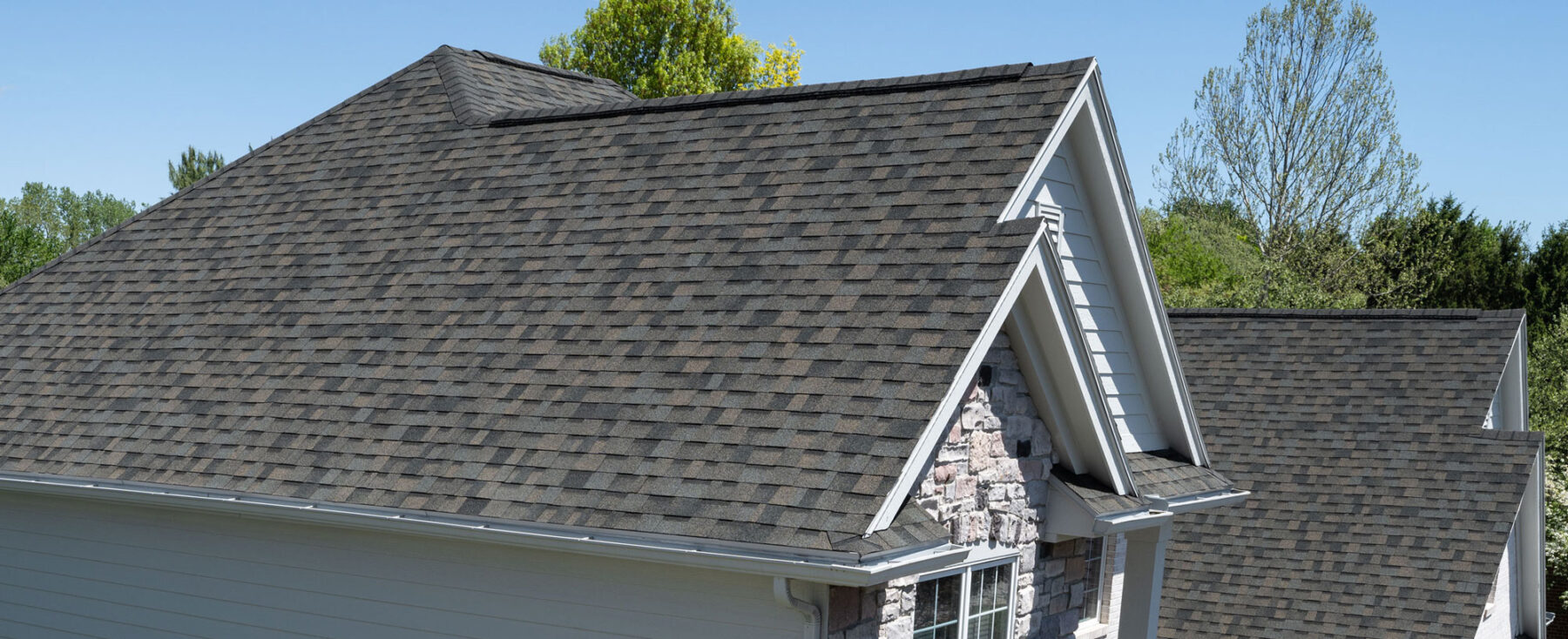
Effective project timeline management and clear communication are crucial for a successful asphalt shingle roofing installation. A well-defined timeline minimizes disruptions and ensures the project progresses smoothly, while open communication fosters trust and allows for proactive problem-solving. Understanding potential delays and having strategies in place for unforeseen issues are also vital components of a successful roofing project.
Sample Project Timeline for Asphalt Shingle Roofing Installation
This sample timeline assumes a typical-sized single-family home and favorable weather conditions. Actual timelines may vary depending on the project’s complexity, size of the roof, and unforeseen circumstances. Always confirm the timeline with your chosen contractor.
Day | Activity |
---|---|
1-2 | Initial site survey and material ordering |
3-4 | Tear-off of old roofing materials (if applicable) and disposal |
5-6 | Roof deck inspection and repairs (if necessary) |
7-8 | Installation of underlayment |
9-10 | Installation of new asphalt shingles |
11 | Installation of flashings, ridges, and vents |
12 | Final cleanup and inspection |
Effective Communication and Coordination with the Contractor
Maintaining consistent and open communication with the contractor is paramount. This includes regular updates on the project’s progress, addressing any concerns promptly, and ensuring all parties are informed of any changes or potential delays.
Effective communication strategies include:
- Establishing a primary point of contact for all communication.
- Scheduling regular check-in meetings or calls to review progress and address any questions or concerns.
- Utilizing email or text messaging for quick updates and clarifications.
- Maintaining detailed records of all communication, including dates, times, and the subject matter.
Managing Potential Project Delays and Unforeseen Issues
Even with meticulous planning, unforeseen issues can arise during a roofing project. These might include unexpected weather delays, material shortages, or the discovery of underlying structural problems. Having a proactive approach to managing these issues is crucial.
Strategies for managing delays and unforeseen issues include:
- Developing a contingency plan that addresses potential delays due to weather or material availability.
- Establishing clear communication protocols for reporting and addressing unforeseen issues.
- Working collaboratively with the contractor to find solutions and minimize the impact of delays.
- Having a backup plan in place, such as alternative materials or scheduling adjustments, to mitigate disruptions.
Material Selection and Quality
Choosing the right asphalt shingles is crucial for a long-lasting, aesthetically pleasing roof. The initial cost of materials significantly impacts the overall project expense, but more importantly, the quality of the shingles directly affects the roof’s lifespan and its ability to withstand the elements. Understanding the different types available and their respective properties is essential for making an informed decision.
Asphalt shingles are the most common roofing material in North America, offering a balance of affordability, durability, and aesthetic versatility. However, not all asphalt shingles are created equal. Significant variations exist in terms of their composition, manufacturing process, and overall quality, leading to considerable differences in performance and longevity.
Types of Asphalt Shingles
Asphalt shingles are broadly categorized into three main types: 3-tab, architectural (dimensional), and luxury shingles. 3-tab shingles are the most economical option, featuring a simple, flat design. Architectural shingles, also known as dimensional shingles, offer a more textured and visually appealing appearance due to their layered design, resulting in a thicker profile and improved durability. Luxury shingles represent the premium segment, often incorporating advanced materials and designs for superior performance and longevity. They frequently feature thicker construction, enhanced weather resistance, and more sophisticated aesthetic features. For example, some luxury shingles might mimic the look of slate or wood shakes.
Factors Influencing Asphalt Shingle Selection
Several key factors should guide your shingle selection process. Durability is paramount; a longer-lasting roof translates to lower long-term costs. Consider the shingle’s lifespan, its resistance to wind damage, and its ability to withstand extreme temperatures and heavy rainfall. The manufacturer’s warranty often provides an indication of expected durability. Aesthetics play a vital role, as the roof significantly impacts the home’s overall curb appeal. Choose a color and style that complements your home’s architecture and personal preferences. Finally, budget considerations are crucial. While higher-quality shingles often come with a higher upfront cost, their extended lifespan can offset this expense over time. Balancing durability, aesthetics, and budget requires careful consideration of the long-term value proposition of each shingle type.
Consequences of Using Low-Quality Materials
Opting for low-quality asphalt shingles can lead to several significant problems. Shingles may degrade prematurely, leading to early cracking, curling, and granule loss. This reduces the roof’s protective capabilities, increasing the risk of leaks, water damage, and structural issues. A compromised roof may require premature repairs or even a complete replacement, leading to unexpected and substantial expenses. Furthermore, low-quality shingles often lack the wind resistance of higher-quality options, increasing the vulnerability of your home to storm damage. This can result in costly repairs and potential insurance claims. Finally, the aesthetic appeal of low-quality shingles often deteriorates quickly, diminishing your home’s curb appeal and potentially impacting its market value.
Warranty and Guarantees
Understanding the warranties offered on your new asphalt shingle roof is crucial for protecting your investment. Warranties provide a safety net against defects in materials or workmanship, ensuring you’re not left with costly repairs shortly after installation. This section clarifies the different types of warranties available and Artikels the claims process.
Asphalt shingle manufacturers typically offer two primary types of warranties: manufacturer warranties and contractor warranties. Manufacturer warranties cover defects in the shingles themselves, such as cracking, granule loss, or premature aging. These warranties usually range from 20 to 50 years, but the specific coverage and terms vary depending on the shingle type and manufacturer. Contractor warranties, on the other hand, cover the workmanship of the installation. These warranties typically cover issues resulting from improper installation, such as leaks or premature shingle failure due to faulty application techniques. The duration of contractor warranties also varies, often ranging from 1 to 10 years.
Manufacturer Warranty Coverage
Manufacturer warranties are usually divided into two parts: a limited warranty covering manufacturing defects and an extended warranty offering additional protection against certain types of damage. The limited warranty typically covers defects that are directly attributable to the manufacturing process, such as faulty materials or flaws in the shingle’s construction. The extended warranty often covers issues like algae growth or wind damage, but usually with some limitations and conditions such as proper ventilation and regular maintenance. For example, a manufacturer might offer a 20-year limited warranty against manufacturing defects and a 30-year extended warranty against granule loss, but only if the roof meets specific ventilation requirements.
Contractor Warranty Coverage
Contractor warranties protect you against problems caused by the roofing contractor’s work. This typically includes issues arising from improper installation, such as leaks around flashing, poorly nailed shingles, or incorrect underlayment application. Unlike manufacturer warranties, which are tied to the shingle product, contractor warranties are specific to the installation performed by a particular company. These warranties often specify what is covered, such as labor costs for repairs, but may exclude damage caused by external factors like severe storms or acts of nature.
Filing a Warranty Claim
The process for filing a warranty claim generally involves contacting both the manufacturer and the contractor. You will typically need to provide documentation, such as photographs of the damage, copies of your purchase agreement and warranty documents, and a detailed description of the problem. The manufacturer will investigate the claim and determine if the damage is covered under their warranty. If the damage is covered by the manufacturer’s warranty, they will usually provide replacement shingles or a reimbursement for repair costs. If the damage is due to faulty installation, the contractor’s warranty will come into play. The contractor is usually responsible for rectifying the problem, often including labor and materials. Many manufacturers require the contractor to handle initial claim processing.
Comparing Warranty Terms and Conditions
Before signing a contract, carefully review the terms and conditions of both the manufacturer’s and contractor’s warranties. Pay close attention to the length of coverage, the types of damage covered, and any exclusions or limitations. Some warranties might have requirements for regular maintenance or inspections to remain valid. For instance, one warranty might cover only manufacturing defects, while another might include coverage for wind damage up to a certain speed. Compare the warranties offered by different contractors and manufacturers to ensure you’re getting the best possible protection for your investment. Consider factors such as the reputation of the manufacturer and contractor, their history of handling warranty claims, and the clarity of their warranty documents. A comprehensive warranty from a reputable company provides greater peace of mind.
Post-Installation Inspection
A thorough post-installation inspection is crucial to ensure the roofing contractor has met the agreed-upon specifications and that your new roof is free from defects. This inspection serves as a final verification step, protecting your investment and identifying any potential problems before they escalate. A timely and detailed inspection can prevent future, more costly repairs.
A comprehensive post-installation inspection involves a systematic review of various aspects of the newly installed roof. This process requires careful observation and attention to detail to detect even minor flaws that could compromise the roof’s longevity and performance. It’s best performed with the contractor present, allowing for immediate clarification and addressing of any concerns.
Roof Surface Examination
This involves a visual examination of the entire roof surface to identify any missing or damaged shingles, uneven shingle placement, exposed nails, or areas where flashing is improperly installed. Look for any signs of granule loss (indicating premature shingle degradation), buckling, or blisters. Pay close attention to valleys, ridges, and around chimneys and vents, which are areas prone to leaks. A detailed inspection should also include checking for proper shingle alignment and overhang. For example, noticeably uneven shingle lines might indicate improper installation techniques, leading to potential water infiltration.
Flashing and Sealants
Proper flashing around chimneys, vents, and other roof penetrations is critical to prevent leaks. Inspect all flashing for proper sealing and secure attachment. Look for gaps, cracks, or areas where sealant may be missing or improperly applied. For instance, a gap around a chimney flashing could allow water to seep into the roof structure. Also examine all sealant points for signs of cracking or separation.
Drainage System Verification
Ensure that gutters and downspouts are properly installed and functioning correctly to prevent water damage. Check for proper slope and alignment to ensure efficient water drainage. Observe whether gutters are securely fastened and free from clogs. Look for signs of water damage around the foundation, indicating possible drainage issues. For example, clogged gutters could lead to water overflowing and damaging the fascia boards or siding.
Checklist for Post-Installation Inspection
Before the inspection, gather necessary tools like binoculars for a better view of high areas, a ladder (if safe and necessary), and a camera to document any issues.
- Examine the entire roof surface for missing or damaged shingles.
- Check for proper shingle alignment and overhang.
- Inspect flashing around chimneys, vents, and other penetrations.
- Verify the proper installation and functionality of gutters and downspouts.
- Check for any exposed nails or staples.
- Inspect for signs of granule loss, buckling, or blisters on shingles.
- Examine the roof’s underlayment (if visible) for any tears or damage.
- Verify the proper installation of ridge vents and soffit vents.
- Check for any signs of water damage around the foundation.
- Review all aspects of the work against the original contract specifications.
Addressing Defects or Issues, Finding the best asphalt shingle roofing contractors nearby
If defects or issues are discovered during the inspection, immediately document them with photographs and detailed notes. Clearly communicate these findings to the contractor, providing specific locations and descriptions of the problems. Work with the contractor to establish a plan for correcting the identified issues. Retain all documentation, including photographs, notes, and communication records. If the contractor is unresponsive or unwilling to rectify the problems, consult your contract and consider further action, possibly involving legal counsel if necessary.
Maintaining Your New Roof
Protecting your investment in a new asphalt shingle roof requires proactive maintenance. Regular care significantly extends the lifespan of your roof, preventing costly repairs and premature replacement. By understanding common problems and implementing a simple maintenance schedule, you can ensure your roof remains a reliable shield for your home for years to come.
Proper roof maintenance involves both routine inspections and occasional more intensive cleaning and repairs. Neglecting these tasks can lead to significant problems that reduce the lifespan of your roof and potentially damage your home’s interior. Early detection of issues is key to preventing larger, more expensive problems down the line.
Regular Roof Inspections
Regular visual inspections are crucial for early detection of potential problems. Ideally, you should inspect your roof twice a year, once in spring after winter’s harsh weather and once in autumn before the winter snows. During these inspections, look for missing, damaged, or curling shingles, signs of moss or algae growth, and any evidence of leaks or water damage. Checking the gutters and downspouts for clogs, which can lead to water damage, is also vital. If you are uncomfortable inspecting your roof yourself, consider hiring a professional roofing contractor for an annual inspection.
Common Asphalt Shingle Roof Problems and Prevention
Several common problems can affect asphalt shingle roofs. Understanding these issues and their prevention is key to extending your roof’s life.
Moss and Algae Growth
Moss and algae can grow on asphalt shingles, particularly in shaded areas with high humidity. This growth can trap moisture, leading to shingle deterioration and premature aging. Regular cleaning with a solution of water and a mild detergent can help prevent and control moss and algae growth. For more persistent growth, a specialized roof cleaning solution may be necessary. Proper ventilation in your attic can also help reduce humidity and discourage growth.
Curling and Cracking Shingles
Exposure to the elements can cause shingles to curl at the edges or crack. This is often accelerated by extreme temperature fluctuations and excessive sun exposure. Choosing high-quality, weather-resistant shingles during installation is the best preventative measure. Regular inspections allow for the timely replacement of damaged shingles before the problem worsens.
Granule Loss
Asphalt shingles are coated with granules that protect them from UV damage. Over time, these granules can be lost due to weathering, foot traffic, or strong winds. Granule loss reduces the shingle’s ability to reflect sunlight and increases its susceptibility to damage. Regular inspections and prompt replacement of damaged shingles are crucial to preventing widespread granule loss.
Leaks and Water Damage
Leaks are a serious problem that can cause significant damage to your home’s interior. They can be caused by damaged shingles, cracked flashing, or clogged gutters. Regular inspections and prompt repairs are essential to prevent leaks and water damage. Addressing any minor leaks immediately is crucial in preventing larger, more costly repairs later.
A Regular Maintenance Schedule for Asphalt Shingle Roofs
A consistent maintenance schedule helps ensure your roof remains in optimal condition.
Recommended Maintenance Schedule
- Spring Inspection: Check for any winter damage, such as missing or damaged shingles, ice dams, or clogged gutters.
- Autumn Inspection: Inspect for any damage caused by summer storms or high winds. Clear gutters and downspouts of leaves and debris to prevent water damage.
- Annual Cleaning: Clean the roof of moss, algae, and debris. Consider professional cleaning for extensive growth.
- Regular Repairs: Address any minor damage, such as cracked or missing shingles, promptly.
Following this simple maintenance schedule can significantly extend the life of your asphalt shingle roof, protecting your home and saving you money on costly repairs in the long run.
Addressing Common Concerns
Asphalt shingle roofing, while durable, is susceptible to damage from weather and age. Understanding common issues and knowing when to seek professional help can save you time, money, and potential further damage. This section addresses prevalent concerns, providing guidance on DIY versus professional intervention and answering frequently asked questions.
Roof Leaks
Roof leaks are a serious concern, potentially leading to significant structural damage and mold growth if left unaddressed. Identifying the source of a leak requires careful inspection, often involving checking flashing around chimneys and vents, inspecting valleys where roof sections meet, and examining the shingles themselves for cracks or missing pieces. Minor leaks, such as those from a single damaged shingle, might be manageable with a DIY repair involving a patching kit. However, larger leaks, persistent leaks, or leaks originating from unknown sources necessitate immediate professional assistance. A qualified roofing contractor possesses the expertise and equipment to locate the source of the leak and implement a lasting repair, preventing further water damage. Attempting complex repairs without proper training and equipment can often worsen the problem, resulting in higher repair costs down the line.
Damaged Shingles
Damaged shingles, such as those cracked, curled, or missing, are common occurrences, especially in areas with harsh weather conditions. Minor shingle damage, such as a few cracked shingles in an inconspicuous area, may be addressed with DIY repairs using appropriate sealant or replacement shingles. However, widespread shingle damage, significant curling or blistering (indicating potential underlying issues), or damage in critical areas like valleys or around chimneys, should be addressed by a professional. A thorough inspection by a roofing contractor can identify the extent of the damage and determine the best course of action, which may involve partial or full roof replacement.
Other Common Issues
Beyond leaks and damaged shingles, other common concerns include: moss or algae growth (which can damage shingles over time and require professional cleaning or treatment), ice dams (which can cause significant damage and require preventative measures), and issues with the flashing or underlayment (which can compromise the roof’s waterproofness and require professional attention). While minor cleaning or preventative maintenance might be DIY-friendly, any issues that affect the structural integrity or waterproofness of the roof require professional assessment and repair.
Frequently Asked Questions
Understanding common questions about asphalt shingle roofing helps homeowners make informed decisions regarding maintenance and repairs.
- How long do asphalt shingles typically last? The lifespan of asphalt shingles varies depending on quality, climate, and maintenance, but typically ranges from 15 to 30 years.
- What are the signs that I need a new roof? Signs include missing or damaged shingles, significant curling or blistering, leaks, persistent moss or algae growth, and sagging in the roofline.
- How much does asphalt shingle roof replacement cost? The cost varies widely based on factors such as roof size, shingle type, labor costs, and location. A reasonable estimate can be obtained from several contractors’ quotes.
- What type of warranty should I expect? Reputable contractors offer warranties on both materials and workmanship, with durations varying depending on the product and the contractor’s policies. It is important to review the warranty details carefully before signing a contract.
- How often should I inspect my roof? Regular inspections, at least twice a year (spring and fall), are recommended to identify and address potential issues early on.
General Inquiries
What is the average lifespan of an asphalt shingle roof?
The lifespan of an asphalt shingle roof typically ranges from 15 to 30 years, depending on the quality of the shingles, installation, and weather conditions.
How can I tell if my roof needs replacing?
Signs of a failing roof include missing or damaged shingles, leaks, curling or buckling shingles, moss or algae growth, and sagging.
What type of warranty should I look for?
Look for both manufacturer and contractor warranties. Manufacturer warranties cover shingle defects, while contractor warranties cover workmanship.
What questions should I ask potential contractors?
Ask about their experience, licensing and insurance, references, project timelines, and payment schedules. Also inquire about their approach to handling potential problems.